Understanding the cost dynamics of accelerator wire is crucial for businesses involved in specialized sectors such as automotive, medical devices, and high-performance electronics. These industries often rely on accelerator wires due to their ability to enhance speed and efficiency in various applications. However, many businesses struggle to navigate the complexities that affect the pricing of these essential components. Here, we delve into the factors influencing accelerator wire costs, providing a comprehensive understanding from experience and industry expertise.
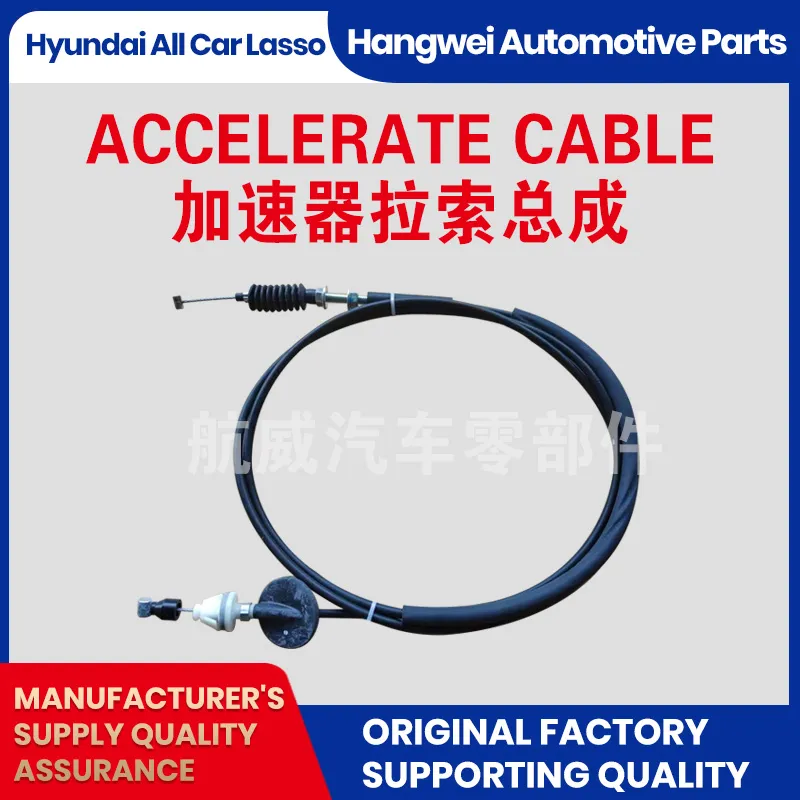
First, material composition plays a pivotal role in determining the cost of accelerator wires. Typically composed of high-grade materials like copper, aluminum, or nickel alloys, the choice of material directly affects pricing. For instance, copper wires, known for excellent electrical conductivity, tend to be more expensive than their aluminum counterparts. Additionally, market fluctuations impacting raw material availability and pricing can lead to significant cost variations.
Manufacturing complexity also contributes to the cost dynamics of accelerator wires. The precision required in wire manufacturing, involving ultra-fine tolerances and specialized coating techniques, can increase production costs. Manufacturers with advanced machinery and technology often charge a premium for their products, reflecting the superior quality and reliability of the wires. Businesses with firsthand experience in the electronics industry can attest to the importance of investing in high-quality wires to minimize downtime and enhance operational efficiency.
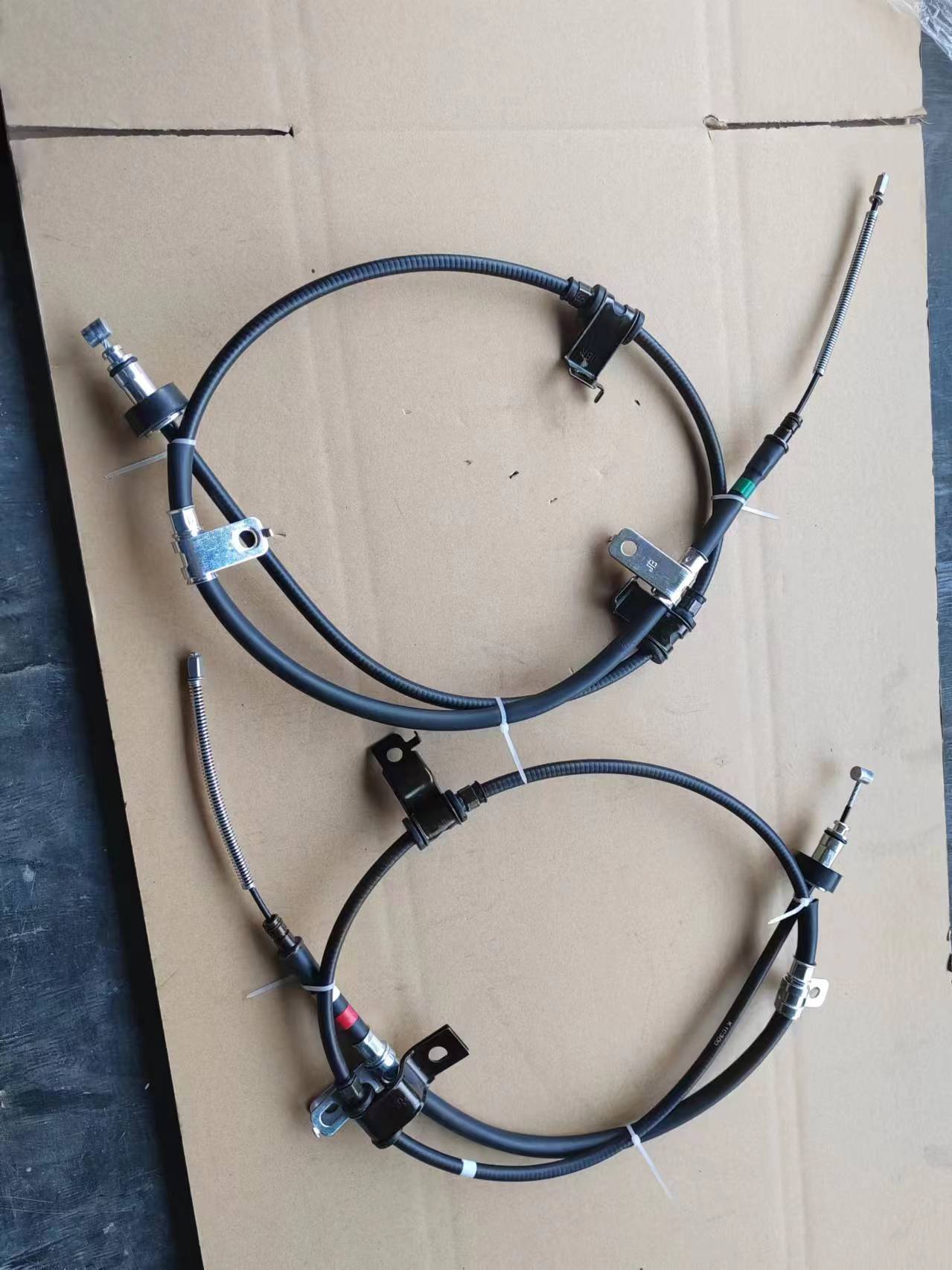
Furthermore,
the customization requirements of accelerator wires can impact costs significantly. Tailored solutions designed to meet specific industry needs, such as resistance to harsh environments or unique dimensional specifications, require additional engineering efforts and resources. Experienced professionals in engineering fields often emphasize the importance of working closely with manufacturers to balance bespoke solutions with cost-effective production strategies.
accelerator wire cost
Regulatory standards are another critical factor influencing accelerator wire costs. Compliance with industry-specific standards, such as those imposed by the International Electrotechnical Commission (IEC) or Underwriters Laboratories (UL), often necessitates rigorous testing and certification processes. Compliance costs, though potentially raising initial expenses, ensure product reliability and safety, translating to long-term savings by avoiding recalls or failures.
Logistics and supply chain considerations are equally important in understanding accelerator wire cost structures. Geopolitical factors, shipping costs, and lead times can affect the total landed cost of importing wires. Experience in global procurement reveals that fostering strong relationships with suppliers and logistical partners can mitigate risks associated with these variables, ensuring uninterrupted supply chains and cost efficiency.
Understanding these multifaceted factors allows businesses to make informed decisions when sourcing accelerator wires. However, it also emphasizes the need for authoritative voices and reliable sources of information. Engaging with industry experts and participating in forums or trade associations can lend valuable insights and foster trustworthiness in supplier relationships.
In conclusion, the cost of accelerator wires is influenced by a combination of material choices, manufacturing complexities, customization demands, regulatory compliances, and supply chain logistics. Businesses equipped with expertise and experience in managing these elements can better navigate the price landscape, ensuring they procure high-quality wires that deliver both cost-efficiency and performance reliability. Such strategic sourcing, backed by authoritative and trustworthy partnerships, can drive innovation and sustained success across industries reliant on accelerator wire technology.