Mastering the Realm of Cable Assembly Clutch Systems An Expert Guide
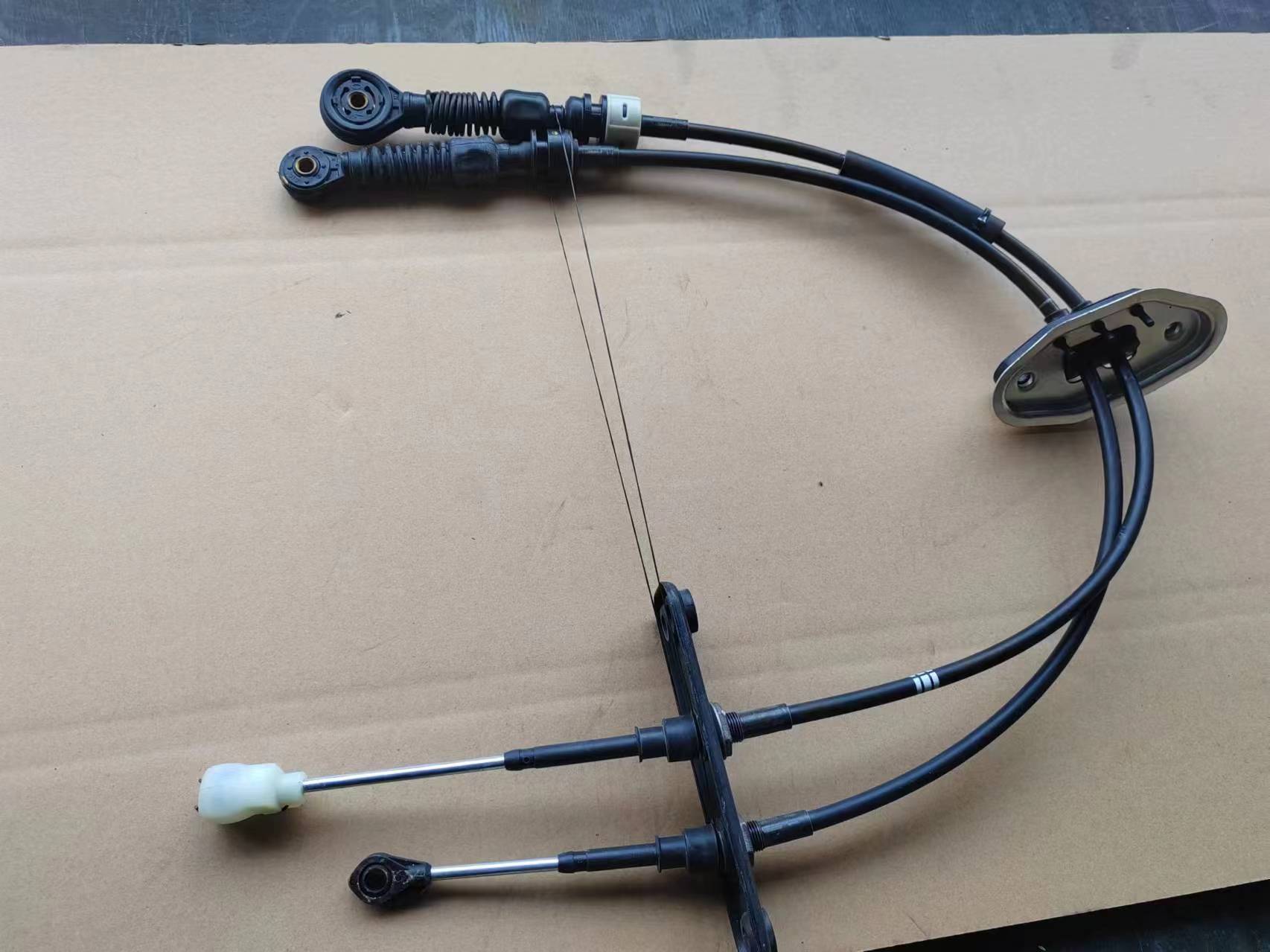
In the intricate world of mechanical systems, the cable assembly clutch is a pivotal player, crucial for the seamless operation of many automobiles and industrial machinery. A deep dive into its mechanisms reveals a part that is not only integral to function but also to innovation within the mechanical domain. This comprehensive guide offers expert insights, uncovering the layers of complexity and highlighting the importance of choosing the right cable assembly clutch for your needs.
Cable assembly clutches are often underappreciated yet indispensable components in the automotive and machinery sectors. Their primary role is to transmit force from the driver's pedal to the clutch mechanism itself, enabling smooth engagement and disengagement of the driveline. Such a task demands precision and resilience, especially in high-performance or heavy-duty applications.
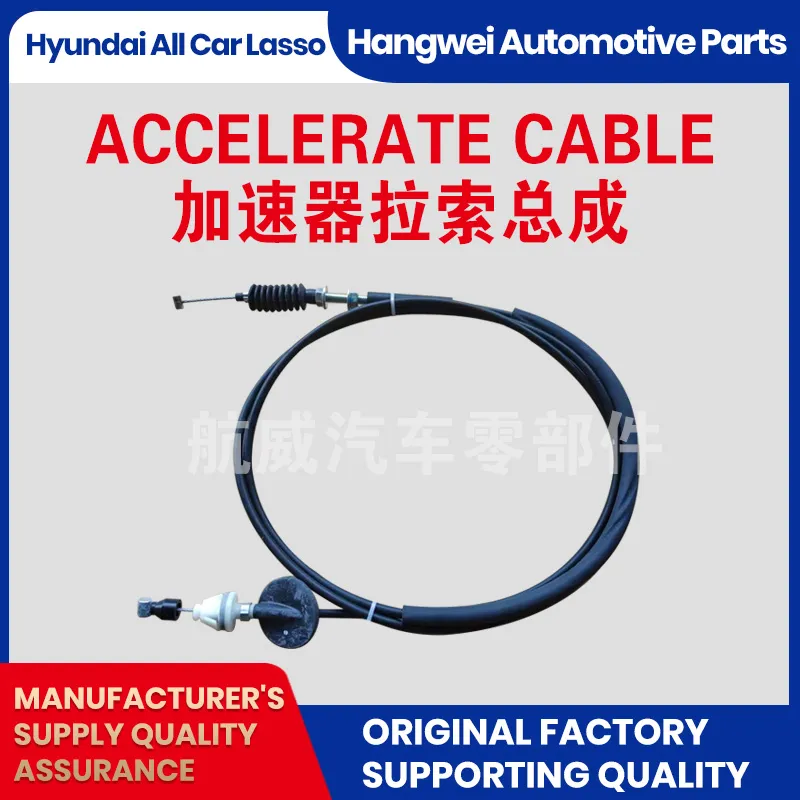
Experience from industry veterans showcases that the choice of material and construction method for a cable assembly clutch directly impacts its longevity and efficiency. High-grade stainless steel and specially formulated polymers are favored for their unmatched resistance to corrosion and wear. These materials ensure that the cable withstands the stresses of daily use, temperature fluctuations, and even exposure to corrosive substances, thereby extending the lifespan of the entire system.
Expertise in the field underscores the importance of regular maintenance and inspection. Technicians recommend routine checks for fraying, slack, and wear, which, if left unattended, can lead to failure and possible downtime. Manufacturers typically advocate for a proactive approach, suggesting replacement based on exposure, mileage, or time-in-service, whichever comes first, rather than waiting for visible signs of deterioration.
cable assy clutch
Recognized authorities in automotive engineering emphasize that the design of a cable assembly clutch is as critical as the materials used. Precision in the manufacturing process, adherence to stringent quality standards, and innovative engineering all contribute to optimal performance. For instance, adjustability is a key feature in advanced cable assemblies, offering the fine-tuning necessary for different vehicular or machinery specifications. This adaptability ensures that the cable can maintain proper tension, providing consistent clutch feel and response.
Trustworthiness in a cable assembly clutch relies heavily on the brand and manufacturer reputation. Well-established manufacturers invest significantly in research and development, ensuring that their products meet industry benchmarks and often exceed customer expectations. Choosing a reputable supplier not only guarantees product quality but also affords peace of mind in terms of warranty and support.
In the pursuit of maximum reliability, aftermarket specialists offer testing and validation services that simulate real-world operating conditions. This service provides an additional layer of assurance, confirming that the cable assembly clutch will perform optimally under the specific demands of its intended application.
The future of cable assembly clutches is poised at the intersection of traditional mechanical engineering and modern technology. As the industry continues to evolve with innovations such as electric actuators and IoT-enabled diagnostics, the humble cable assembly clutch is not left behind. Engineers are exploring new frontiers with hybrid designs that incorporate both cable and electronic components, striving for enhanced efficiency and control.
Understanding the essence of cable assembly clutches extends beyond their role as mere mechanical components. They are dynamic parts of a larger system that, with the right expertise, setup, and maintenance, ensure the seamless operation of vehicles and machinery alike. For those invested in automotive or industrial maintenance, having a nuanced grasp of these assemblies can translate into significant improvements in performance and reliability, ultimately leading to cost savings and reduced operational downtime.