Handbrake cables are an essential component in vehicle safety systems, ensuring that a vehicle remains stationary when parked. Properly functioning handbrake cables are crucial for preventing accidents caused by vehicles rolling away, especially on inclines. With advancements in technology and engineering, the production and innovation behind handbrake cables have evolved significantly, ensuring enhanced safety and performance.
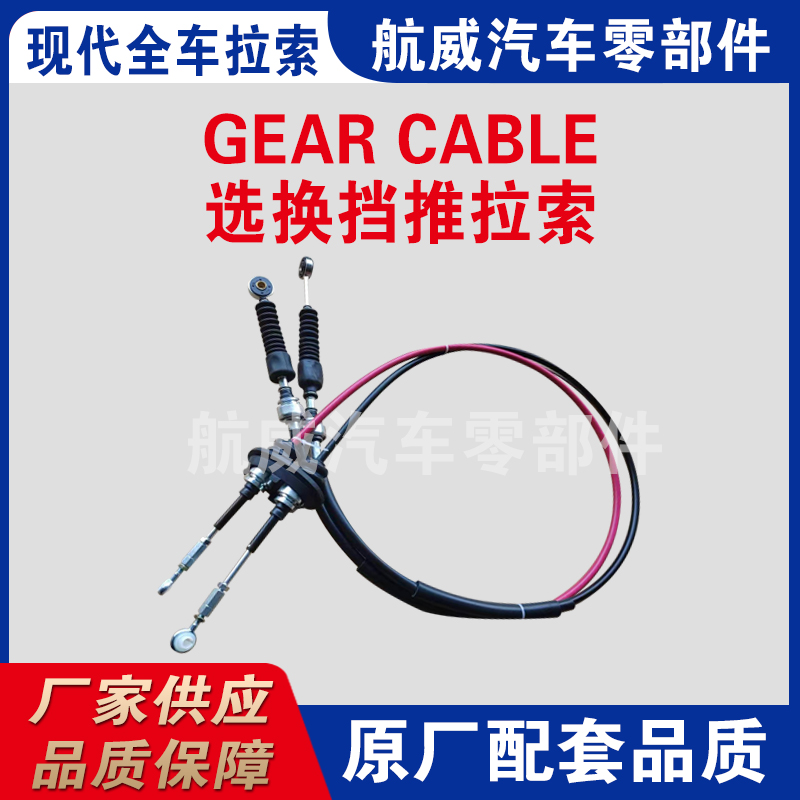
In recent years, advancements in materials have greatly influenced handbrake cable manufacturing. New composite materials are being used, providing greater strength and durability compared to traditional steel cables. These materials offer superb resistance to environmental factors such as moisture, salt, and temperature fluctuations, ensuring longevity even in harsh conditions. This not only extends the life of the product but also provides reliability for drivers, reducing the likelihood of brake failure.
A critical aspect of handbrake cable design is flexibility combined with robust tensile strength. This ensures smooth operation and firm engagement of the brake system. Innovations in cable design now focus on reducing friction within the cable sheath, allowing for quicker and more reliable engagement and disengagement. Manufacturers achieve this through specialized coatings and lubricants applied during the production process, augmenting the overall performance of the handbrake system.
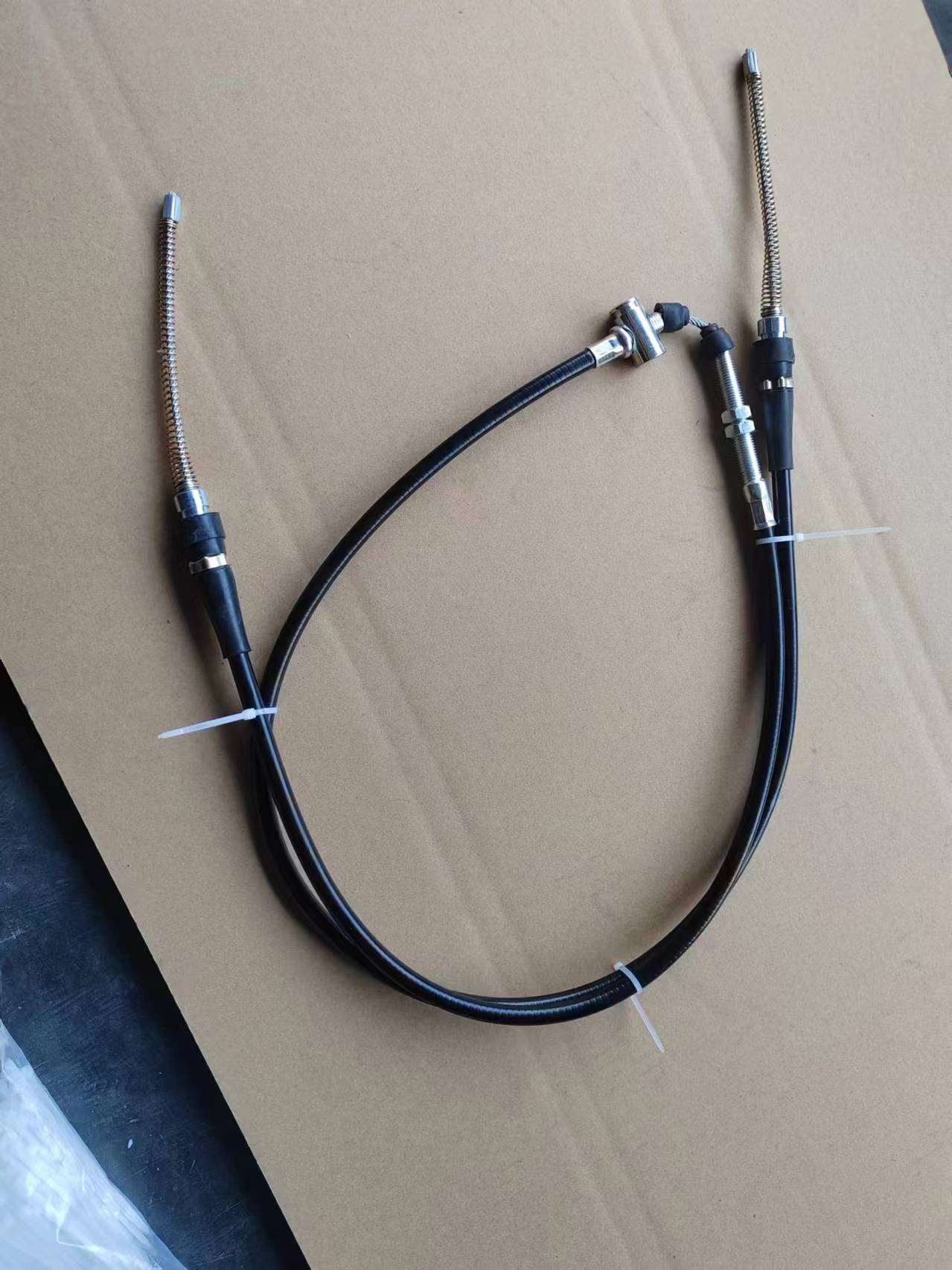
Precision engineering plays an integral role in the manufacture of handbrake cables. Each cable is meticulously designed to meet specific standards and tolerances. This precision engineering ensures that every cable fits impeccably within the braking system, delivering consistent performance across various vehicle types and models. Utilization of CNC machines and automated processes also ensures that each handbrake cable maintains a high standard of quality, reducing human error and variability in production.
In line with sustainable practices, many manufacturers are now adopting eco-friendly production methods. This includes the use of recyclable materials and the implementation of environmentally friendly processes that reduce waste and energy consumption. Such practices not only benefit the environment but also enhance the reputation of manufacturers who prioritize sustainability, aligning with consumer preferences for green products.
handbrake cables made
Handbrake cable manufacturers often operate under stringent regulatory standards. Compliance with these regulations is crucial, as it guarantees the safety and reliability of the product. ISO certification and other quality assurance processes are integrated into manufacturing to ensure adherence to safety guidelines. These certifications provide customers with the assurance that the products they are using meet global safety and quality benchmarks.
For vehicle owners, understanding the importance of maintaining and replacing handbrake cables is vital. Regular inspections can prevent potential failures, ensuring the safety of all occupants. It is advisable for vehicle owners to consult with professional automotive technicians for assessments and replacements, ensuring that the parts used meet original equipment manufacturer (OEM) specifications.
The expertise and craftsmanship involved in making handbrake cables reflect a comprehensive understanding of automotive safety requirements and engineering excellence. Manufacturers invest heavily in research and development to offer solutions that enhance braking performance and driver confidence. As vehicles continue to advance with technology, handbrake cable systems will also evolve, integrating smarter technologies for enhanced safety features, such as electronic parking brakes.
In conclusion, the innovation and meticulous engineering of handbrake cables underscore their critical role in automotive safety. As manufacturers continue to push the boundaries of technology and material science, the reliability and performance of handbrake cables are set to improve, giving vehicle owners peace of mind. Keeping abreast of these innovations is essential for both manufacturers and consumers to ensure safety in the ever-evolving landscape of automotive design.