In the modern mechanical and automotive industries, the need for precision and efficiency has given rise to innovative solutions that ensure smooth operation of machinery. Among these solutions, the in line clutch plays a pivotal role, offering distinct advantages that enhance machine performance. This article delves into the nature of in line clutches, their applications, and the benefits they render to various industries.
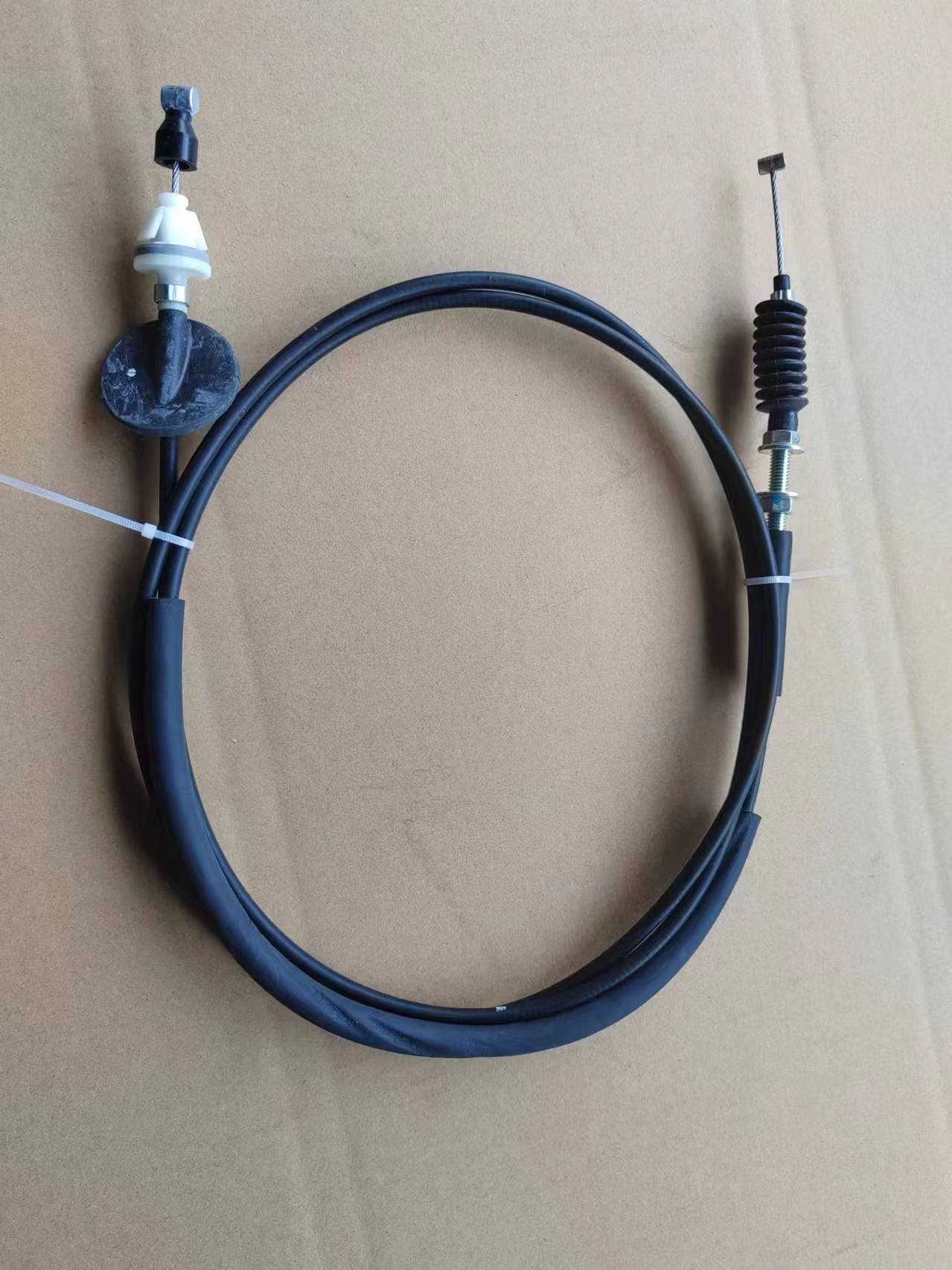
An in line clutch is specifically designed to transmit torque between two aligned shafts. Unlike traditional clutches, which are often bulky and require significant space, in line clutches are compact and can be integrated seamlessly into the system’s design. This space-saving quality is crucial for applications where size constraints are a significant consideration, such as in automotive and aerospace industries where every inch and pound matter for performance and efficiency.
The primary function of an in line clutch is to engage and disengage the engine from the drivetrain's rotating shafts. This allows for controlled power transmission,
protecting the machinery from shock loads, and preventing mechanical overloads. One of the most prominent applications is in precision manufacturing, where in line clutches are used to ensure that the machinery does not suffer from excessive wear and tear, thereby extending the equipment's lifespan.
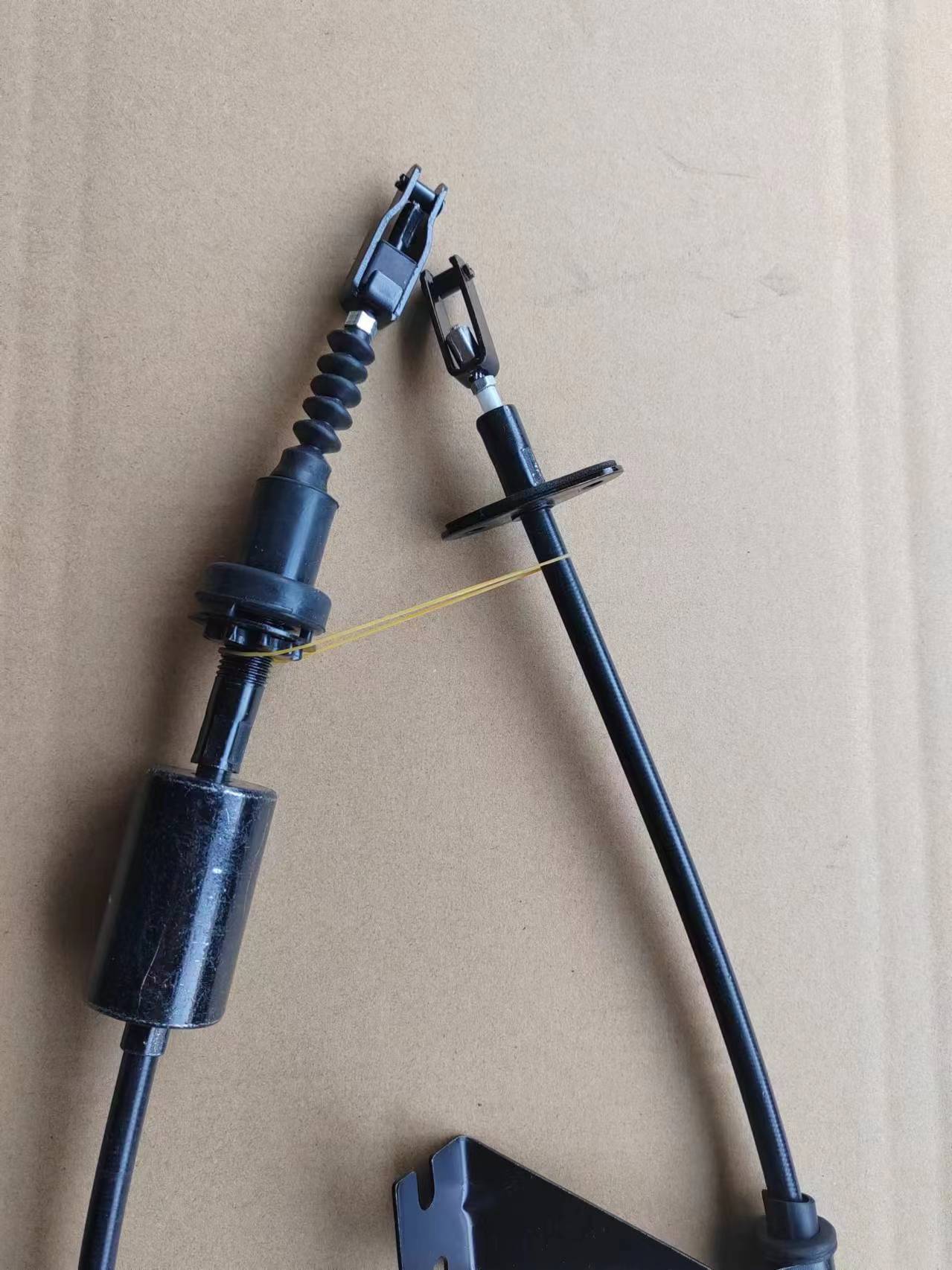
Industry experts highlight the importance of an in line clutch’s ability to improve operational efficiency. The engagement and disengagement process is quick and seamless, minimizing downtime, and maintaining continuous operation. For example, in conveyor systems, in line clutches can be crucial in applications requiring frequent stops and starts, allowing for precise control over the movement of goods. This is particularly beneficial in sectors like food processing and packaging, where precision and hygiene are paramount.
In addition to efficiency, the reliability of in line clutches contributes to their authoritative use in demanding environments. Many in line clutches are designed to withstand harsh industrial conditions, including high temperatures and exposure to corrosive substances. This durability is achieved through material choice and design innovations, such as the use of high-strength alloys and protective coatings. As a result, in line clutches can operate effectively with minimal maintenance, reducing the overall cost of ownership for businesses.
in line clutch
The expertise behind in line clutch manufacturing ensures that these components meet stringent quality standards. Renowned manufacturers invest heavily in research and development to produce clutches that not only perform efficiently but also ensure safety. The use of computer-aided design (CAD) and rigorous testing protocols enables manufacturers to deliver products that can be trusted in critical applications, from heavy machinery to precision instrumentation.
From a safety perspective, in line clutches add an extra layer of protection against mechanical failure. By controlling torque and allowing for rapid disconnection of power, they help in preventing potential accidents caused by machine malfunction. This aspect has become increasingly important in industrial settings where safety regulations are stringent and compliance is non-negotiable.
Furthermore, the integration of advanced technologies, such as electronic control and monitoring systems, has enhanced the capability and functionality of in line clutches. Intelligent in line clutches can communicate real-time data to centralized control systems, providing insights into performance metrics and identifying potential issues before they escalate. This capability represents a leap forward in predictive maintenance, allowing companies to proactively address maintenance needs, thus enhancing trustworthiness in critical operations.
Moreover, the adaptability of in line clutches makes them a versatile component, capable of customization to suit specific industry needs. Whether used in a high-torque application in construction machinery or in the delicate environment of an automated laboratory process, in line clutches can be engineered to deliver optimal performance.
In conclusion, the adoption of in line clutches within various industrial applications is a testament to their exceptional ability to enhance machine functionality and reliability. Through experience and expertise, manufacturers continue to innovate, providing solutions that offer authoritative performance and trusted operation. As industries evolve, the demand for such advanced components will only grow, making in line clutches a cornerstone of modern machine design and operation. Businesses seeking to optimize their machinery’s performance should consider the integration of in line clutches as a strategic move towards future-proofing their operations.